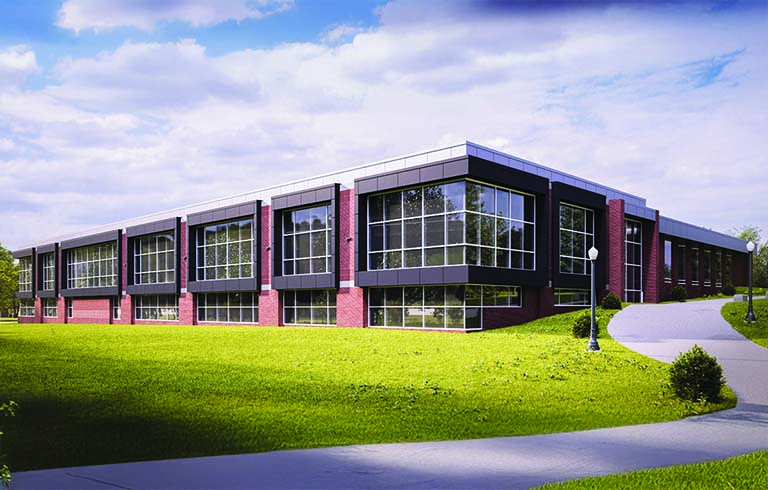
Trine University receives contribution from Honda toward Pellegrino Center
Trine University has received a $100,000 contribution from Honda toward its new John and Mary Pellegrino Student Design and Training Center (Pellegrino Center).
April 15, 2024
A Trine University senior design team hopes their project can someday help reduce that trauma.
Currently, medical personnel set the nail using a targeting jig manufactured by OrthoPediatrics. The nail requires screws at the top and bottom to hold it in place, but the jig only provides alignment for the top screw.
The group, comprised of biomedical engineering majors Collin Hawes of Indianapolis, Jacob Long of Edon, Ohio, Christopher Smith of Kokomo, Indiana, and Kayla Stoeffler of Fishers, Indiana, designed an attachment for the jig that provides alignment for the bottom screw hole, no matter the size of the nail.
Taking on a challenge, helping kids
The project came about following an internship Long completed at OrthoPediatrics in the summer of 2023. Biomedical engineering professor John Patton, Ph.D., asked Long to see if the company would be interested in sponsoring a senior design project.
Hawes and Smith both chose the project because they felt it was the most challenging assignment available.
“I think it's really about taking on the challenge and learning what it means to be an engineer in the orthopedic industry,” Hawes said.
Stoeffler said the project appealed to her because she has worked extensively with children.
“Getting an opportunity to work in an orthopedic device company that specifically works for children is very cool,” she said. “It really aligns with my passion, so this kind of project was right up my alley.”
The literature Stoeffler reviewed showed that the alignment process for the bottom screw can require from 14 to 30 X-rays.
“With it being in the middle of an operating room, they don't have a whole lot of protection equipment, because that's going to introduce items that need to be sterilized or can't be sterilized,” she said. “Both surgeons and patients are getting exposed to a lot of X-ray radiation through the procedure.”
Precise and adjustable
OrthoPediatrics tasked the team with developing a solution that would eliminate most, if not all, of the need for X-rays and provide more precision in setting the bottom screw.
It also needed to accommodate a wide range of nail sizes and body types.
“When these nails are being inserted, everyone's anatomy is different and there's a lot of force going into it, so sometimes there can be a little bit of deflection,” Long said. “The device has to be able to have more room for adjustment than just a simple fixed part.”
The group spent the fall semester developing initial concepts based around electronic sensors. The team later found those designs conflicted with established surgical procedures.
They went back to the drawing board at the beginning of the spring semester — when most senior design groups are beginning product fabrication — to design a prototype that used mechanical means. The entire process included back-and-forth conversations with OrthoPediatrics regarding design features.
“All the parts were modeled in CAD, originally,” said Stoeffler. “We used this to develop and do basic tests, such as finite element analysis, to determine the amount of stress required or applied, and how much deflection would occur.”
The group also used CAD to design drive mechanisms and determine where to position gears.
The final prototype attaches to the lower end of the OrthoPediatrics jig and includes a telescoping arm system that allows for different lengths of nails and a guide that helps steady the drill bit for creating screw holes.
The team said OrthoPediatrics has suggested that future iterations of the device feature fewer, larger adjustment knobs. The group also hopes future student design teams will investigate different options for materials.
“The project had many difficult challenges to overcome,” said Smith, “but through our combined skillsets and experience we were able to engineer a novel targeting device that we can be proud of.”